The intense summer heat is wreaking havoc on Southwest Airlines flights, causing soda cans to burst and leading to injuries among flight attendants. The airline confirmed on Wednesday that there have been numerous incidents of carbonated drink cans rupturing, often while being opened, resulting in onboard messes and approximately 20 injuries to employees so far this summer.
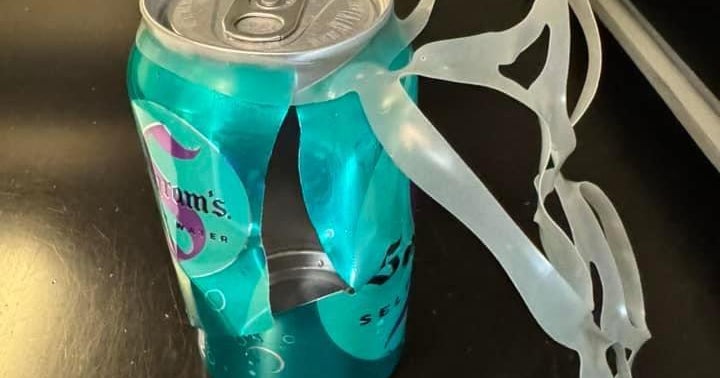
Heat-Induced Soda Can Bursts Cause Injuries
These injuries, including hand injuries that required stitches, have brought increased attention to the issue, as it appears to be happening more frequently this year compared to last. Southwest Airlines officials acknowledged the problem, stating they are actively working to address it, especially in some of the hotter provisioning locations such as Austin, Dallas, Houston, Phoenix, Las Vegas, and Sacramento. Chris Perry, a Southwest spokesperson, mentioned that the airline has been “communicating to our employees about it throughout the spring and summer” and has developed a mitigation plan to tackle the problem.
Southwest Airlines Implements Mitigation Strategies
The root of the issue may lie in how Southwest stores and loads drinks onto planes in extreme heat. Unlike other airlines, Southwest does not use air-conditioned catering trucks to deliver meals and drinks to the aircraft, resulting in more frequent exposure of drinks to outside temperatures. An internal email from July 12, obtained by CBS News, detailed procedural changes to address the problem, especially in hot weather locations.
The changes include stocking fewer cans on provisioning trucks to minimize the time the cans spend in the heat, placing carbonated drinks in coolers on trucks, monitoring truck and can temperatures with thermometers, and not boarding products when outside temperatures are known to elevate the risk of bursting cans. Additionally, employees have been advised not to open cans that are noticeably hot to the touch or appear deformed due to heat exposure.
Future Plans to Prevent Soda Can Bursting
Despite these measures, Southwest Airlines acknowledges that more immediate solutions are necessary. The airline has now halted the onboarding of cans with a temperature of 98 degrees or more, with beverages at or above this temperature being returned to the warehouse for cooling. The airline is also considering positioning refrigerated trailers at its warehouses to keep cans cool before loading them onto provisioning trucks.
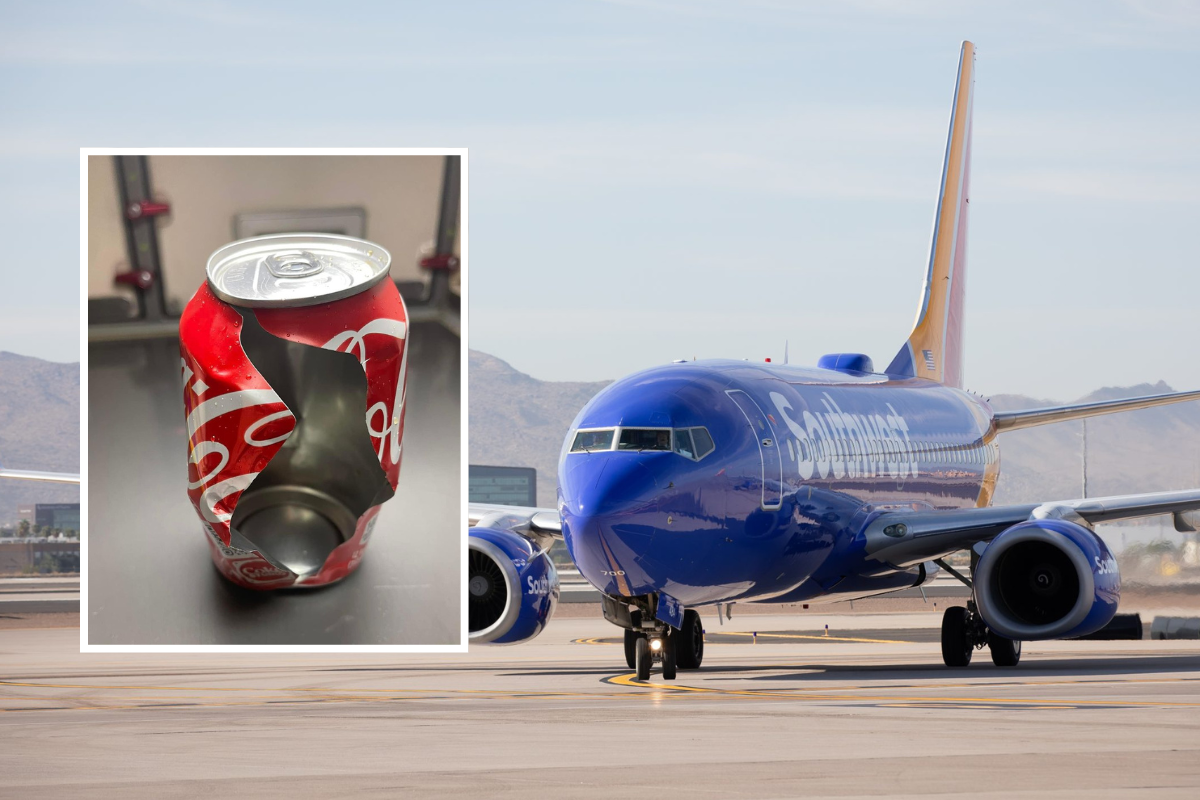
Southwest has begun testing air-conditioned provisioning trucks and is in discussions with Coca-Cola to evaluate the current cans and consider alternatives, such as a smaller 7.5-ounce option. In Arizona and Nevada, cans are being marked to identify if they originated from refrigerated or non-refrigerated trucks as part of the testing process. Meanwhile, pictures of burst cans are circulating online in Facebook groups dedicated to Southwest employees, with many expressing frustration and concerns over safety. Southwest Airlines operates about 4,200 flights daily, and ensuring the safety and well-being of both employees and passengers remains a top priority as the airline navigates these heat-related challenges.